Phase 1 of the project involved the project team developing an entire ship model capable of being assessed with AMT’s Finite Element Software package (Altair). This phase of the task was aided with AMT’s deep understanding of the Anzac Class Platform (from its original designer role) and AMT’s experience in large scale FEA models. The model was created in Rhino 6 and included structural details for all bulkheads, primary structure, decks, deck stiffening, hull stiffening, tanks and pillars.
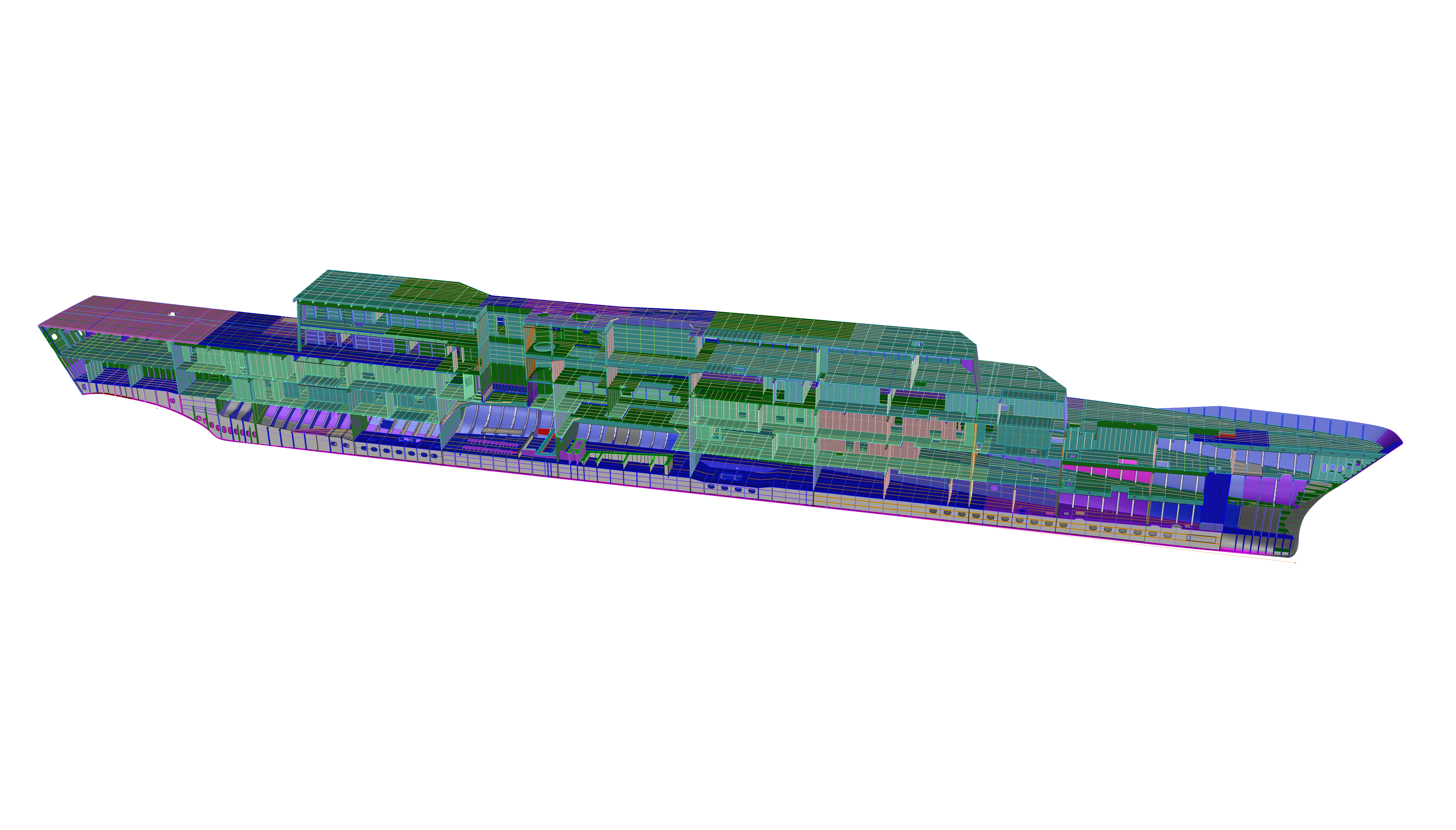
Figure 1: Anzac Class FEM Section View
In preparation for the FEA of the ship, AMT developed rule-based loads that would be used to induce the wave, equipment, self-weight, buoyancy and slamming loads onto the model. The
assessment replicated a “worst case” loading onto the vessel inducing hogging and sagging with two load cases to simulate the operational cycle of the vessel. Along with calculating the aforementioned loads, AMT developed a practical method to apply the combination of what became 574 unique loads for the assessment.
The assessment produced the largest Finite Element Model (so far) to be developed by AMT and highlighted AMT’s capabilities to conduct global ship assessments using FEA techniques. The investigation also pushed the limits of the software using a mesh size suitable for smaller localised models, with 59,700 individual surfaces being meshed with over 2.5 Million elements.
The second phase of the investigation was the assessment of the Frigate for longitudinal strength and fatigue life. The investigation of the platform proved to be extremely successful with a number of interesting findings, importantly with the confirmation that the platform is very capable in terms of longitudinal strength and resistant to fatigue. The assessment helped the customer understand the capabilities of the platform and the limitations in terms of the service life and displacement.
Figure 2: Anzac Class FEA Indicative Stress Plot
Share Article